JMJ
Greetings and welcome!
In our last episode (September 2022 for cryin’ out loud), most everything was here or on its way. It seemed that rebuilding was about to begin. One major item that had yet to arrive was the Crankcase Bearing Remover and Installer (JIMS #1672). The thinking here was that we might as well put in new bearings while we have the engine in pieces. I ordered one shortly before the September blog post. Soon after the post, I learned that this tool would be delayed. After searching other sources, all of which were out of stock, I resigned myself to wait.
And wait. And wait. In fact, after three separate extensions (read “delays”), I contacted JIMS directly to learn that a new production run of this tool would be scheduled at some point, but no dates. When the fourth delay notice arrived, I decided to take a different approach.
Using my fancy new electronic caliper, I took measurements of bearings and crankcases to design my own tool. The concept was pretty clear. With plans in hand (thanks to a Mechanical Drawing class that I took as a freshman), I went to my local machine shop. Following a brief discussion with the owner, it looked like I would be waiting as long or longer for my custom tool because of the incredible backlog of work. That was disappointing.
As the concept marinated in my imagination, it occurred to me that there were bound to be other combinations of supports and drivers that would allow me to swap these bearings. Reviewing the measurements, I concluded that a piece of 3-inch pipe and a 1-13/16-inch socket would get the job done. It all came together on November 1, 2022.
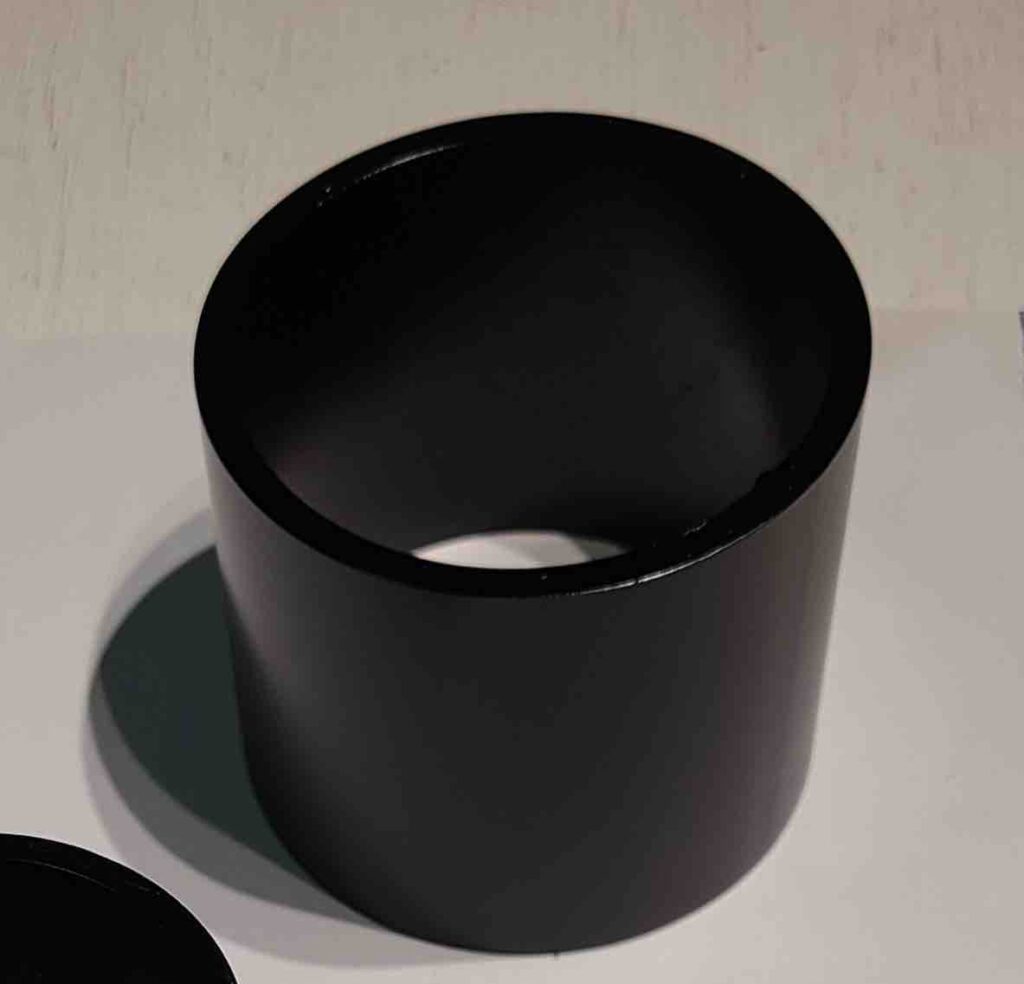
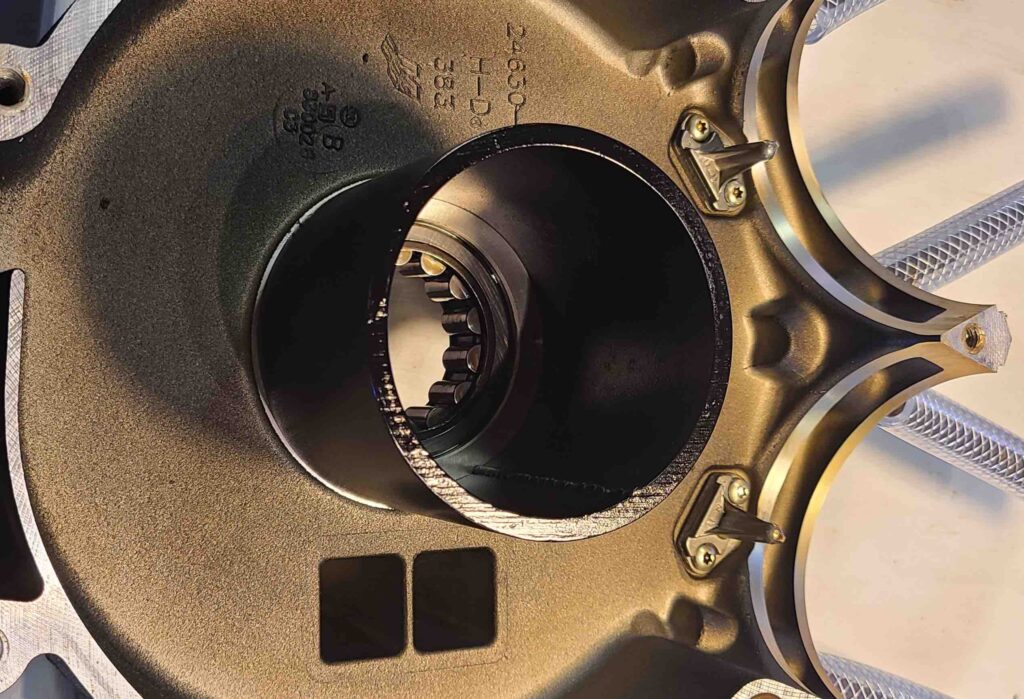
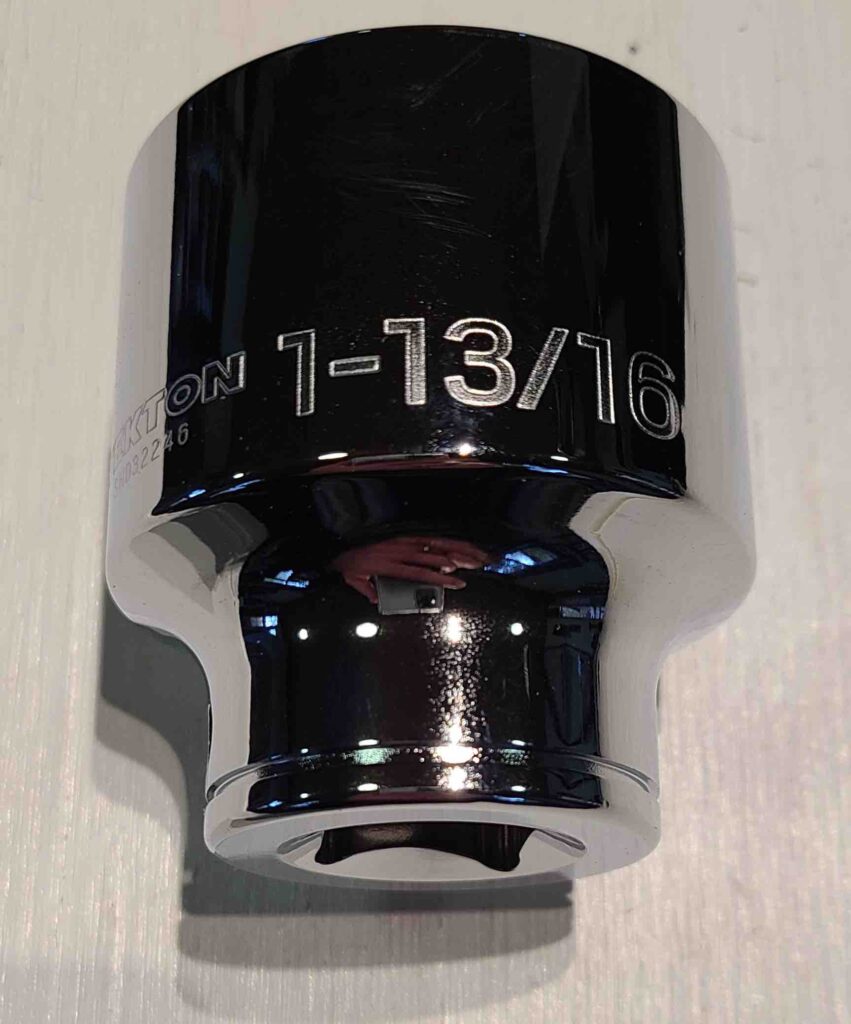
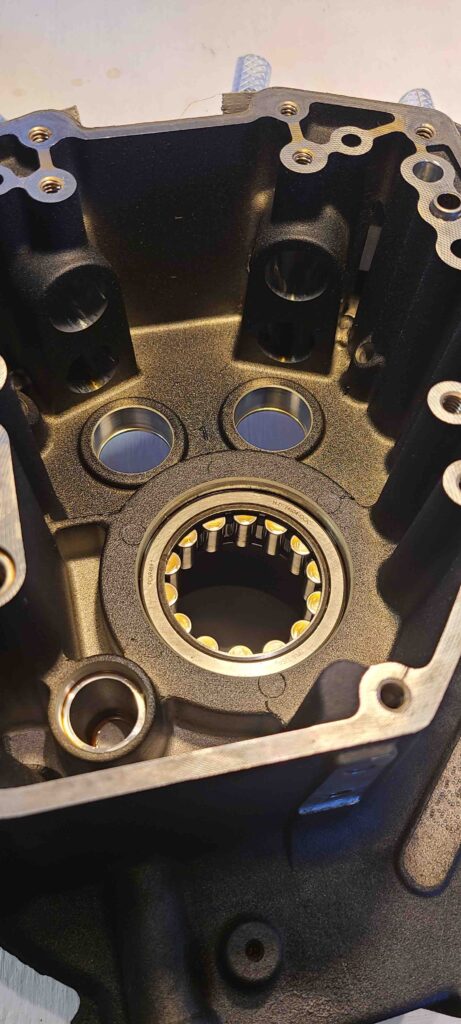
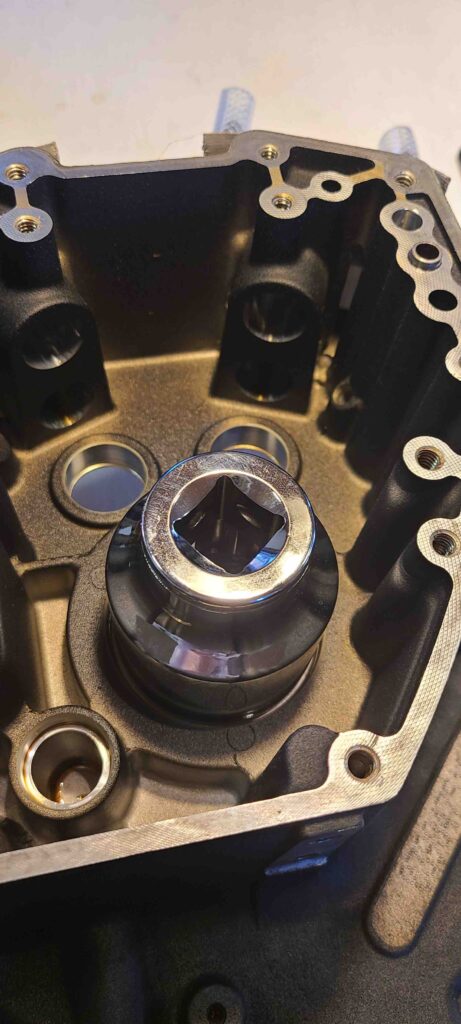
Here’s the stack-up. One section of 3-inch pipe that was three inches long on the bolster plates of the hydraulic press.
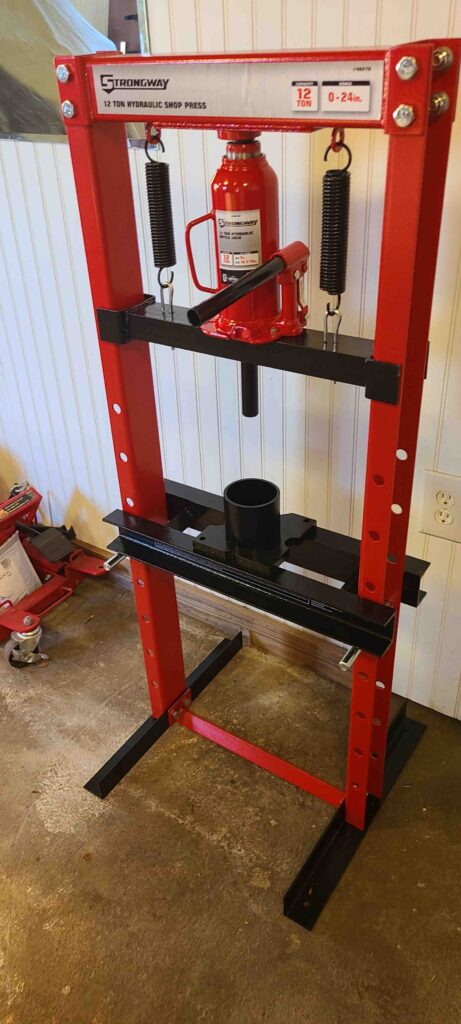
Left Crankcase Half positioned over the pipe.
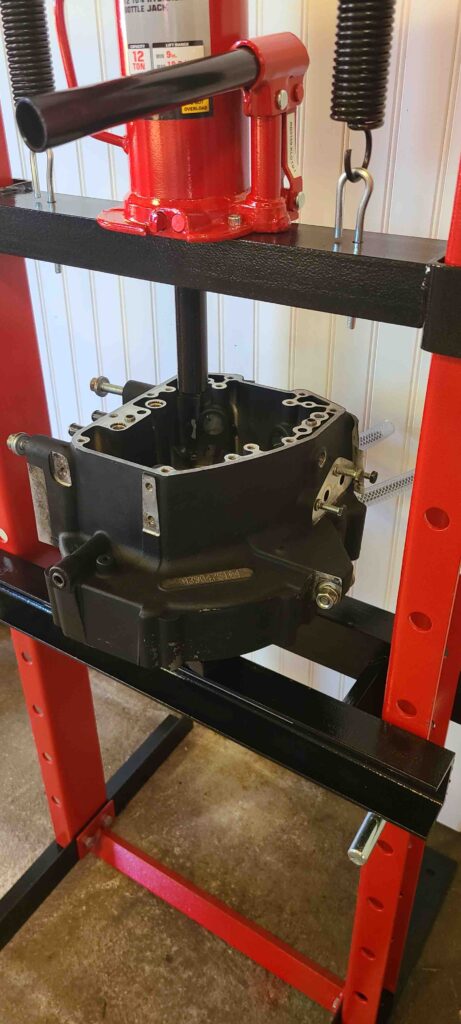
1-13/16-inch socket on the bearing. I also put a washer (not shown in the photo) on top of the socket to engage the ram.
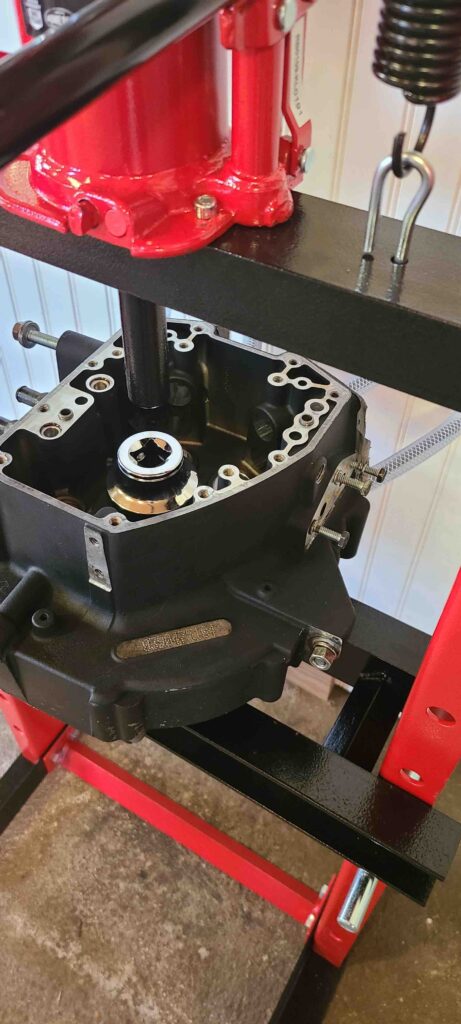
And then we pressed.
I was pretty pleased with the results until I examined the crankcase half. As seen in the photos below, the final release of the bearing caused a fracture on the lip of the case.
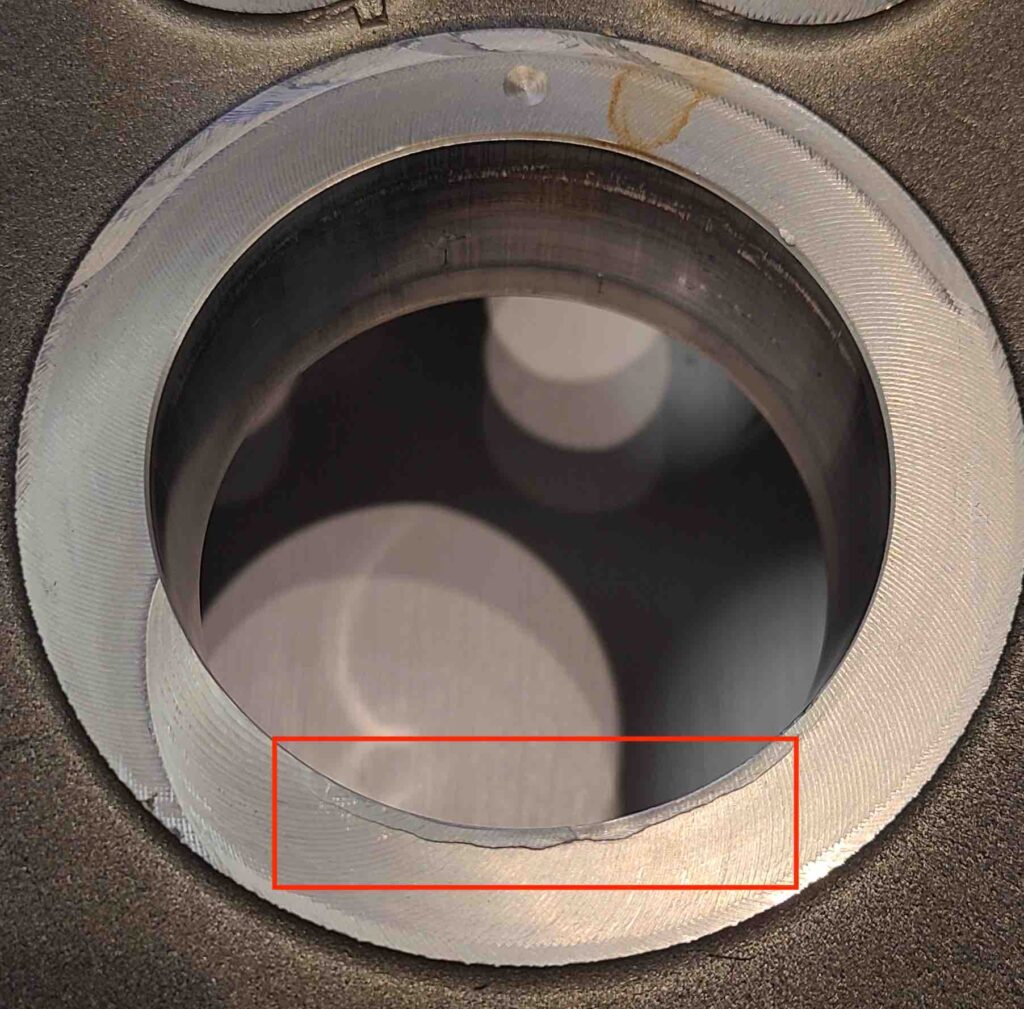
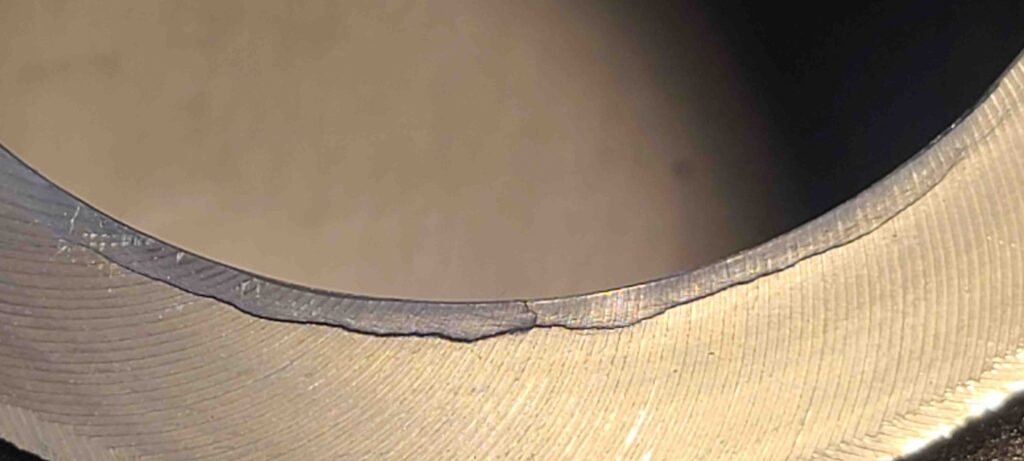
After putting the tools away, I went inside to sulk, convinced I was now looking at buying a new crankcase.
A new crankcase (sold as a mated pair) listed for $1,570 – plenty of motivation to find a solution. Taking measurements of the damaged area on the surface, it looked like the damage might be removed while leaving the entire surface area for the bearing’s outer casing. Back to the machine shop.
Fortunately, the owner of the machine shop was an old Harley guy and understood exactly what I wanted when I asked him to mill out the damage leaving a slight bevel. We didn’t know if the fracture went deeper into the casing, but he was willing to try. After some waiting (backlogged work), I got the call in February 2023 that the crankcase was ready. The results were excellent.
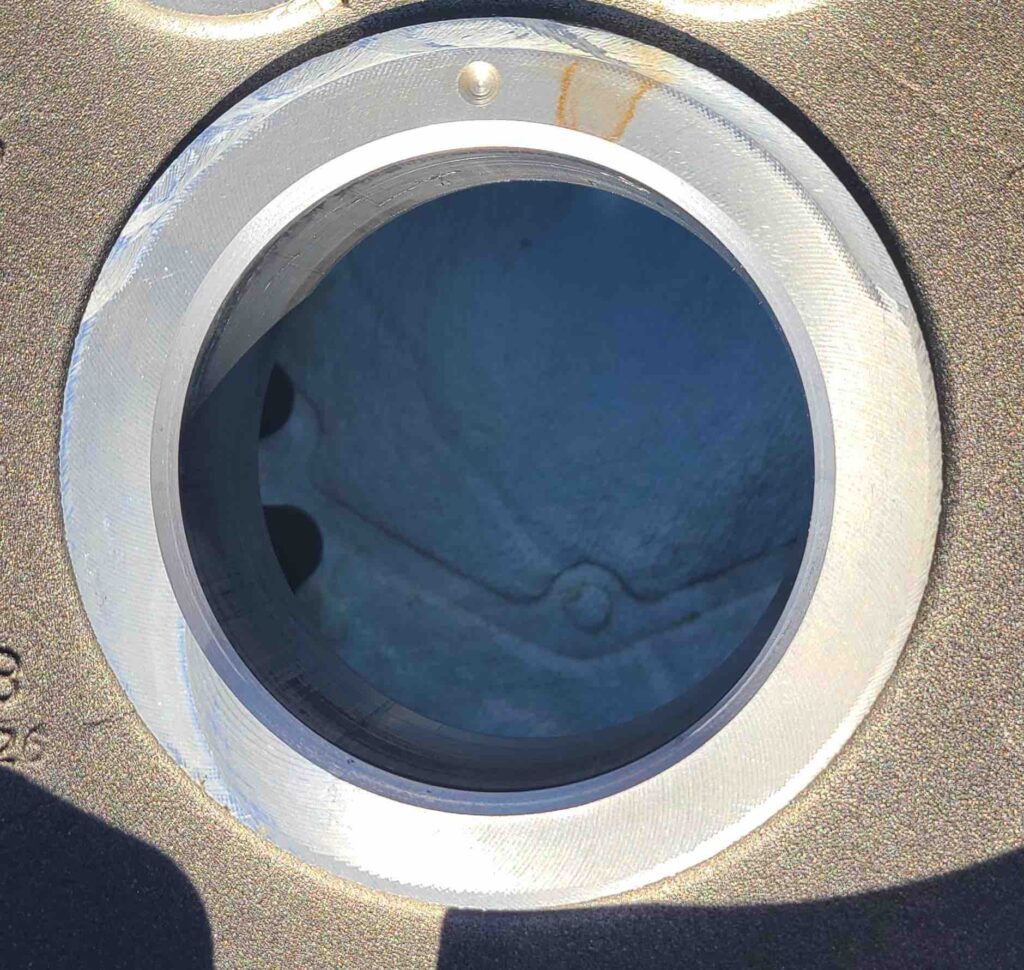
The larger problem of installing the new bearing in the Left Crankcase Half and then dealing with the Right Crankcase Half was still a problem, but things were looking positive again.
I have met people who refuse to wear brand merchandise (e.g., hats, jackets, shirts, etc.) to avoid giving Harley-Davidson free advertising. This always struck me as odd, but it’s a free country. When I see someone in HD apparel, I use it as an opportunity to open a conversation about motorcycling, in general, and Harleys, in particular. This is exactly what happened when I met an electrician at a job site wearing a hat. One thing led to another and suddenly I had a name and number for a shop that could take care of the bearing swap. Thank you, Lord, for throwing me a clue and introducing Antonio.
To wrap this up, we now have new bearings installed in both crankcase halves and are ready to begin reassembly.
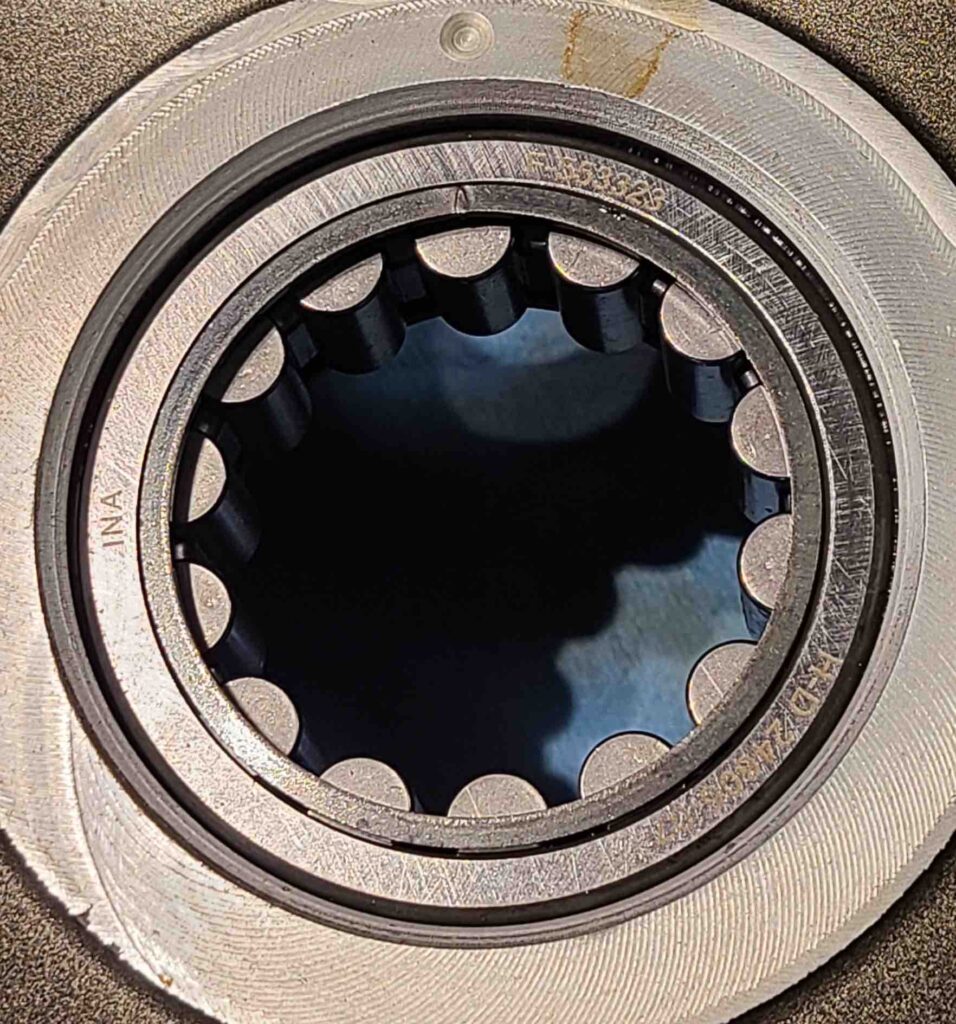
Best wishes and don’t forget to feed the seagulls!
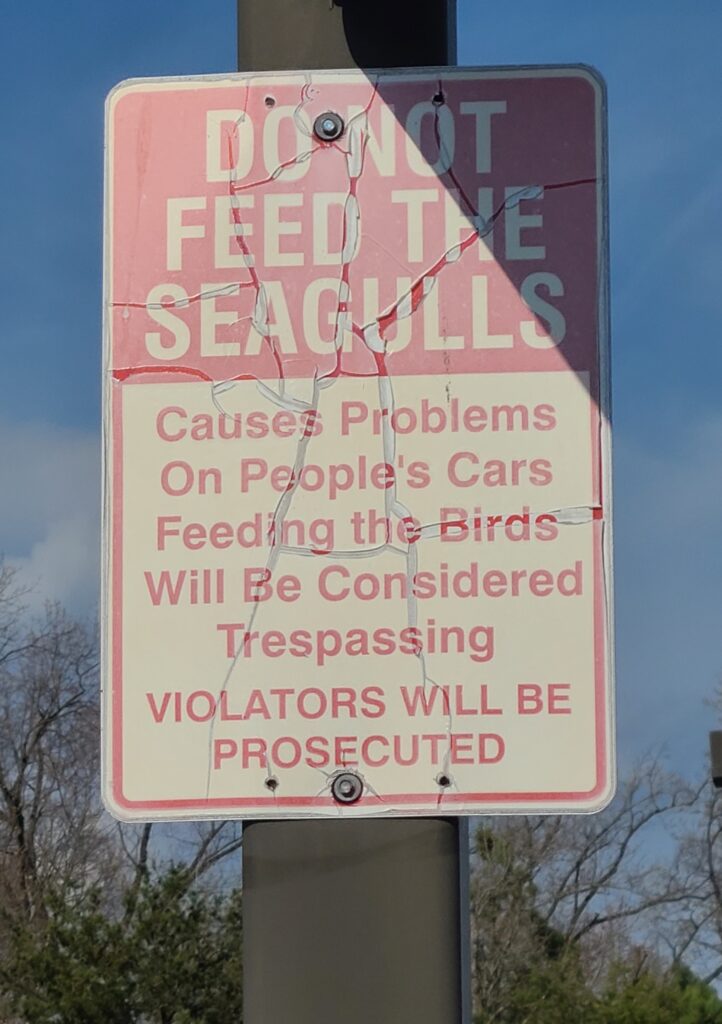